CAD Projects
Bringing ideas into reality.
Helical Wind Turbine
This project represents a significant endeavor within my CAD portfolio, showcasing my dedication and expertise in renewable energy technology. Approximately one year ago, I embarked on a mission to engineer a wind turbine capable of supplying electricity to a single household.
My journey began with extensive research into various types of wind turbines, assessing their respective characteristics, limitations, and suitability for my objectives. After careful consideration, I determined that a helical vertical axis wind turbine offered the optimal balance of efficiency, adaptability, and performance. Helical turbines, renowned for their superior energy efficiency compared to other models, exhibit exceptional resilience in turbulent wind conditions, making them ideal for urban environments.
With a clear vision, I transitioned to the design phase, focusing on creating a turbine that could be easily replicated using a medium-sized 3D printer. Beginning with a scaled-down prototype, I conducted comprehensive testing and analysis to refine the design iteratively. Each iteration incorporated improvements informed by real-world experimentation, ensuring a robust and reliable final product.
The blade design for the helical wind turbine has been finalized, marking a significant milestone in the project's development. However, work continues refining the gearbox and generator components using SOLIDWORKS software.
Originating in May 2023 and initially conceptualized within FreeCAD, this project underscores my commitment to innovation and renewable energy technology.
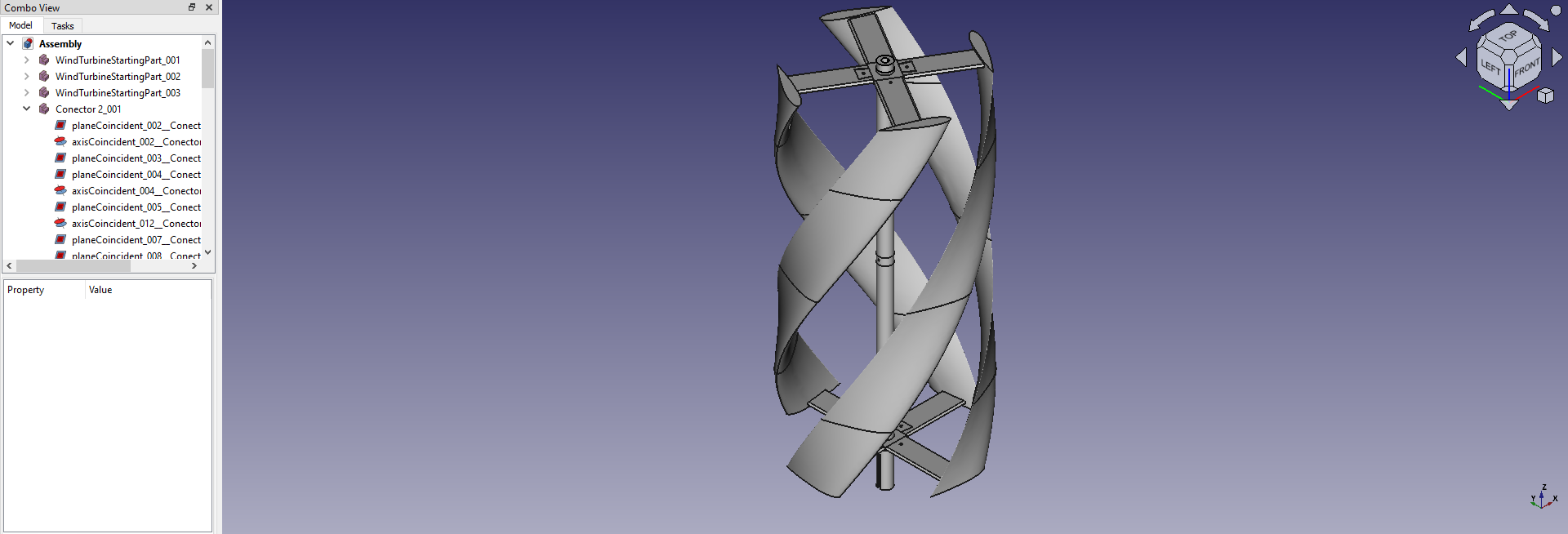
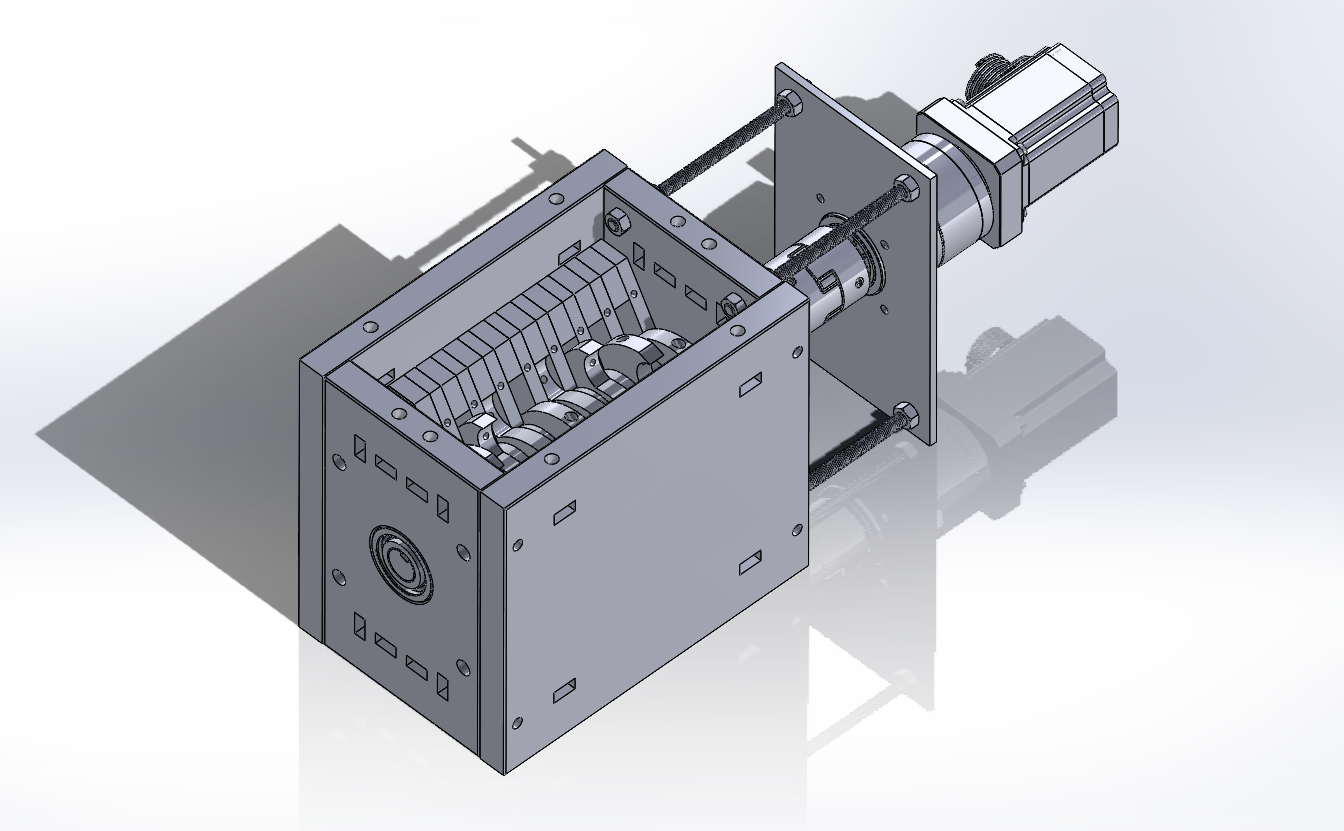
Plastic Shredder
This project represents a significant milestone in my portfolio, ranking as one of my largest endeavors. Over the years, my work in 3D printing has accumulated kilograms of support filament, failed prints, and discarded part designs. Recognizing the value of these materials and the potential for recycling, I sought to develop a solution for repurposing them back into usable filament.
Motivated by sustainability and resource efficiency, I designed and constructed a filament shredder. This crucial component transforms bulky support structures and failed prints into finely shredded material suitable for extrusion into new filament rolls. Notably, this project marked my first foray into incorporating metal components, necessitating collaboration with CNC machining specialists and online procurement to acquire essential parts.
Initiated in August 2023 using the FreeCAD program and completed in September 2024 using SOLIDWORKS, this endeavor showcases my ability to innovate and engineer solutions to complex challenges while highlighting my commitment to environmental responsibility.
Expandable Ant Nest
As a designer at Globallink
Company, I spearheaded the development of an innovative ant nest design tailored to meet the needs of the ant-keeping community. Drawing from my experience as an ant keeper, I recognized the demand for expandable ant nests. These nests offer a practical solution for ant colonies that grow over time, eliminating the inconvenience of relocating entire colonies between nests of varying sizes.
The design I conceptualized features a modular framework enabling seamless attachment of expansion modules to all four sides of the nest. This customizable approach empowers users to effortlessly adjust and scale their colony size according to their requirements. Following approval from the company, we successfully produced over 10,000 units of this expandable ant nest model.
Utilizing FreeCAD, I developed this design in February 2023, aligning with Globallink's commitment to innovation and customer-centric product development.
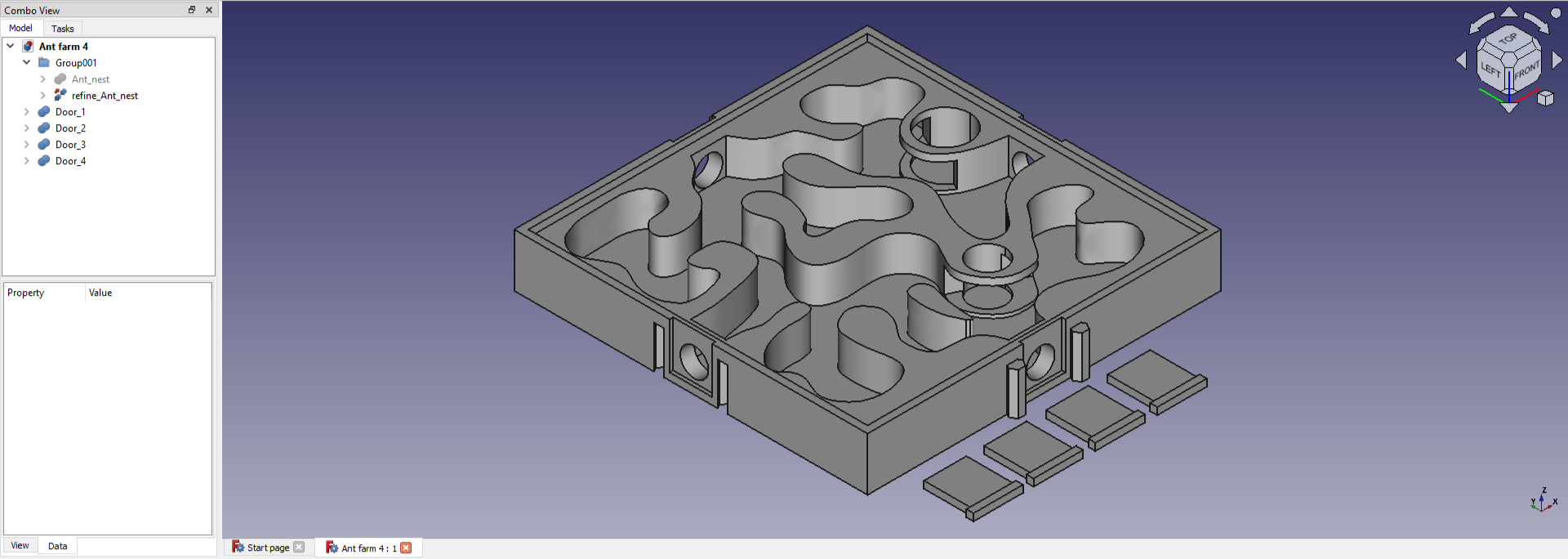
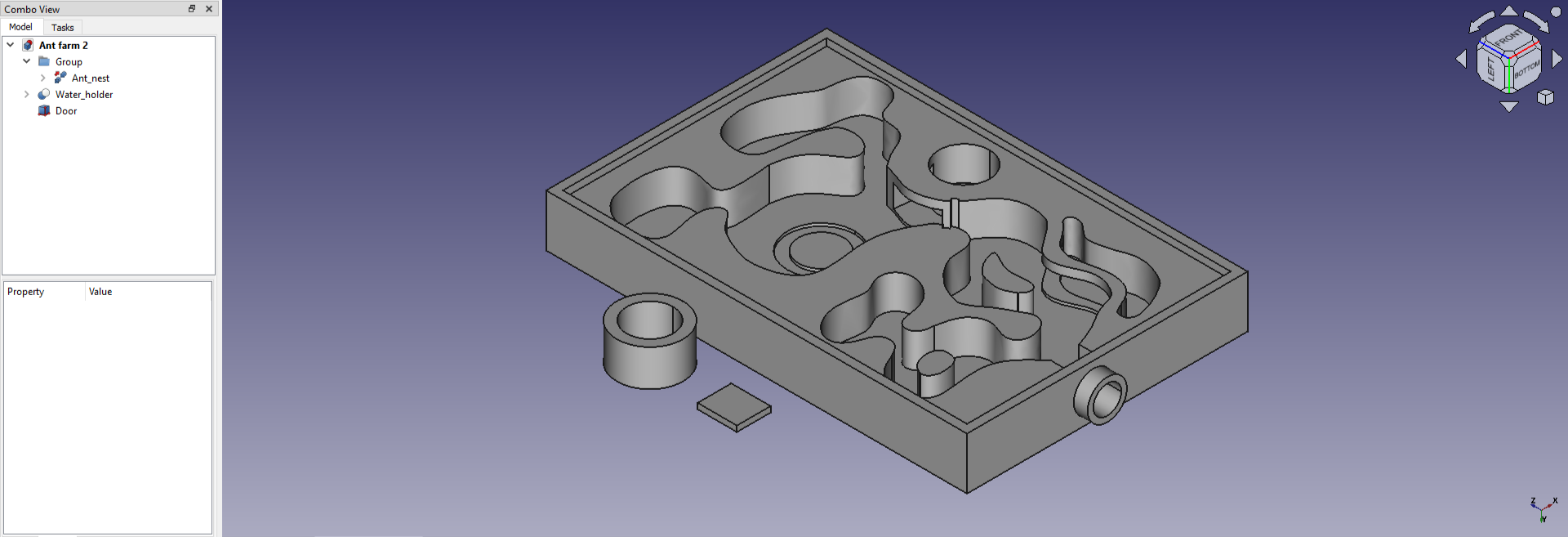
Semi Expendable Ant Nest
This ant farm model is part of a series developed for Globallink Company, showcasing innovative designs aimed at accommodating expanding ant colonies. Unlike conventional ant nest configurations, this model offers a specialized habitat tailored for colonies reaching a predetermined size limit. Inspired by natural environments, the design features narrow passages and chambers to emulate authentic ant habitats. Created in February 2023 using FreeCAD, this model demonstrates a commitment to precision and functionality.
Test Tubes Holder
I developed this model as part of my portfolio to showcase my expertise in designing solutions for practical challenges. The inspiration behind this project stems from my passion for ant-keeping, particularly managing a large fire ant colony that annually produces hundreds of new males and queens. In captivity, ensuring the comfort and well-being of the queen ants during their crucial post-mating phase is paramount.
Traditionally, housing queen ants in individual test tubes poses logistical challenges, particularly in maintaining stability and minimizing stress. To address this, I utilized my skills in FreeCAD to design specialized supports for the test tubes. These supports provide a secure and stress-free environment for the queens by incorporating features such as stability and ease of access.
Developed in August 2023, this model stands as a testament to my dedication to craftsmanship and problem-solving in design.
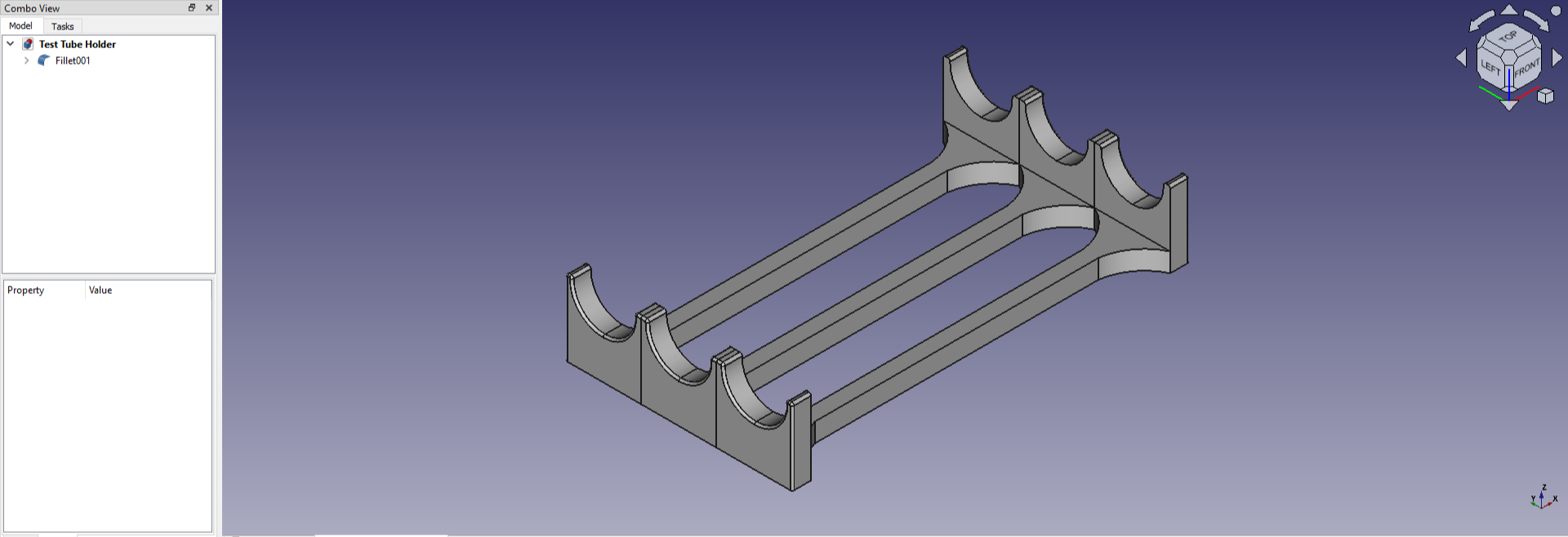
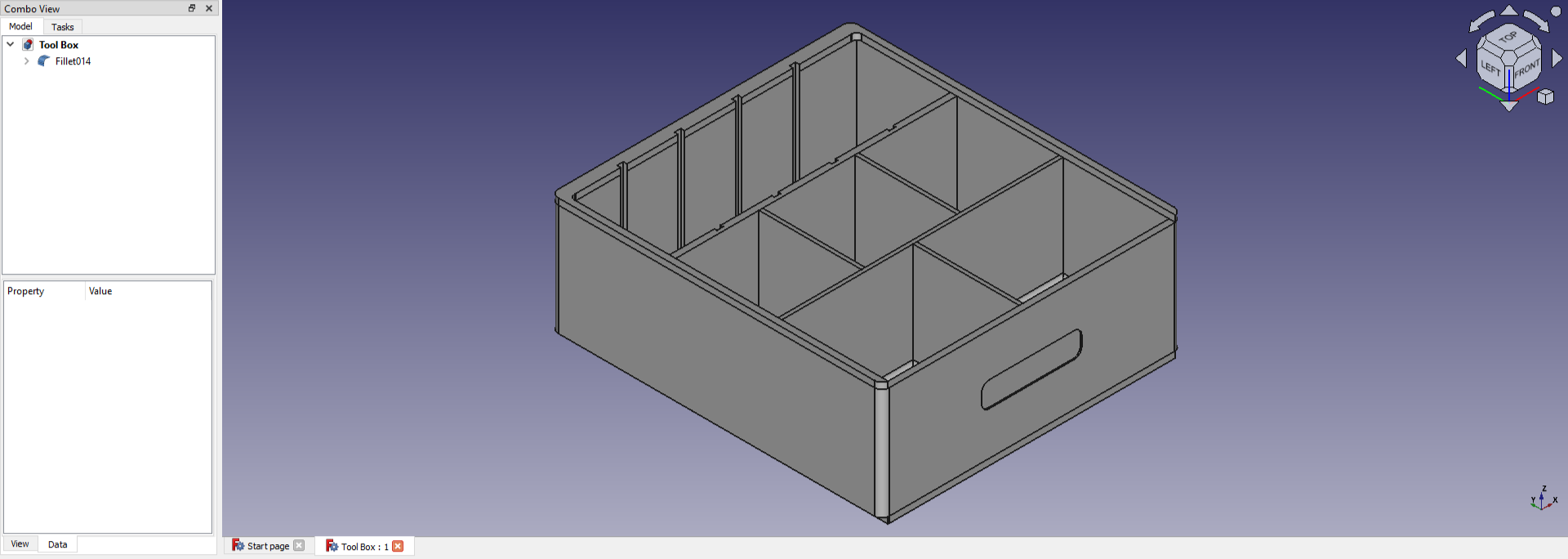
Tool Organizer
As part of a product design initiative for Globallink Company, I created an efficient organizer for fasteners and tools. The project involved iterative design processes to meet the company's specific requirements and expectations. The final model was refined through multiple design iterations and feedback sessions to achieve optimal functionality and user satisfaction.
The approved design, finalized in August 2023, seamlessly integrates user-friendly features and ergonomic considerations.
This project exemplifies my ability to collaborate with clients, iterate on designs, and deliver innovative solutions tailored to each project's unique needs.
nd CaseInterior design clothing
This project represents another iteration of enhancements made to the CR-10 printer. The primary issue addressed was the frequent clogging of the 3D printer's nozzles, leading to print failures. Upon investigation, it was determined that the root cause of this problem lay in a gap between the Teflon liner and the heat break, resulting in filament buildup and subsequent obstruction of filament flow. Additionally, the heat sink failed to adequately maintain the filament's solid state, often leading to filament overflow. I procured and installed a new nozzle, heat sink, and filament feeding system to resolve these issues. The entire extrusion mechanism was custom-built, necessitating the design of a bespoke casing. This model was developed using FreeCAD in September 2023.
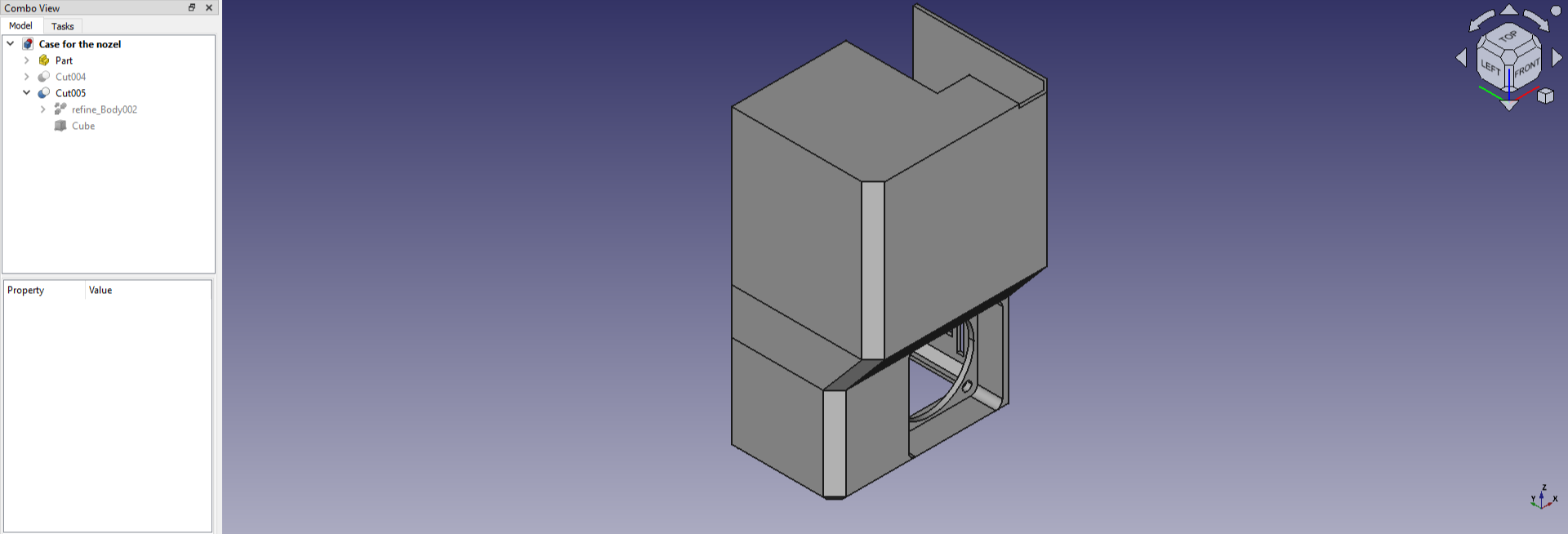
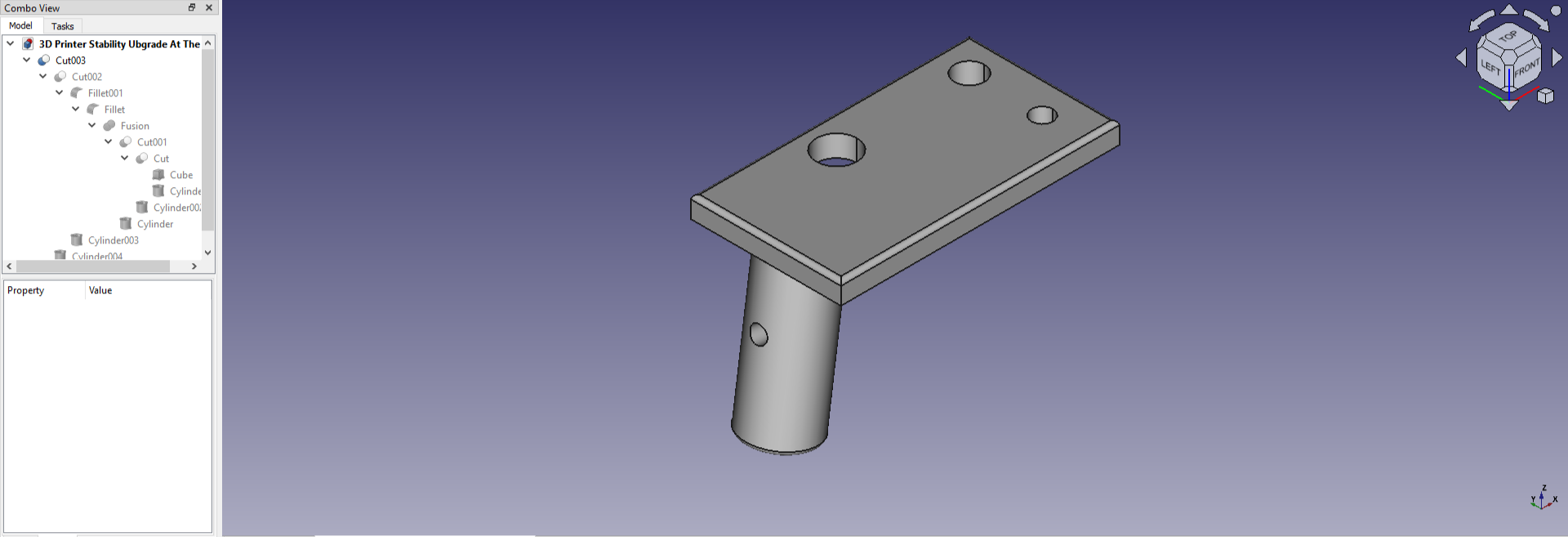
Top Support Joint
In pursuit of enhancing the performance of my CR-10 3D printer, which has been in operation for five years, I embarked on a design endeavor. The printer encountered stability issues during the production of tall models, resulting in undesirable surface textures on the upper layers. To address this challenge, I conceptualized and engineered a support connector. This component, crafted to link the upper and lower sections of the 3D printer with a metal pipe, aimed to augment its stability during operation. Subsequently, utilizing the same 3D printer, I fabricated the designed model and seamlessly integrated the upgrade into the existing system. Both design iterations were meticulously crafted using FreeCAD software in August 2023.
Bottom Support Joint
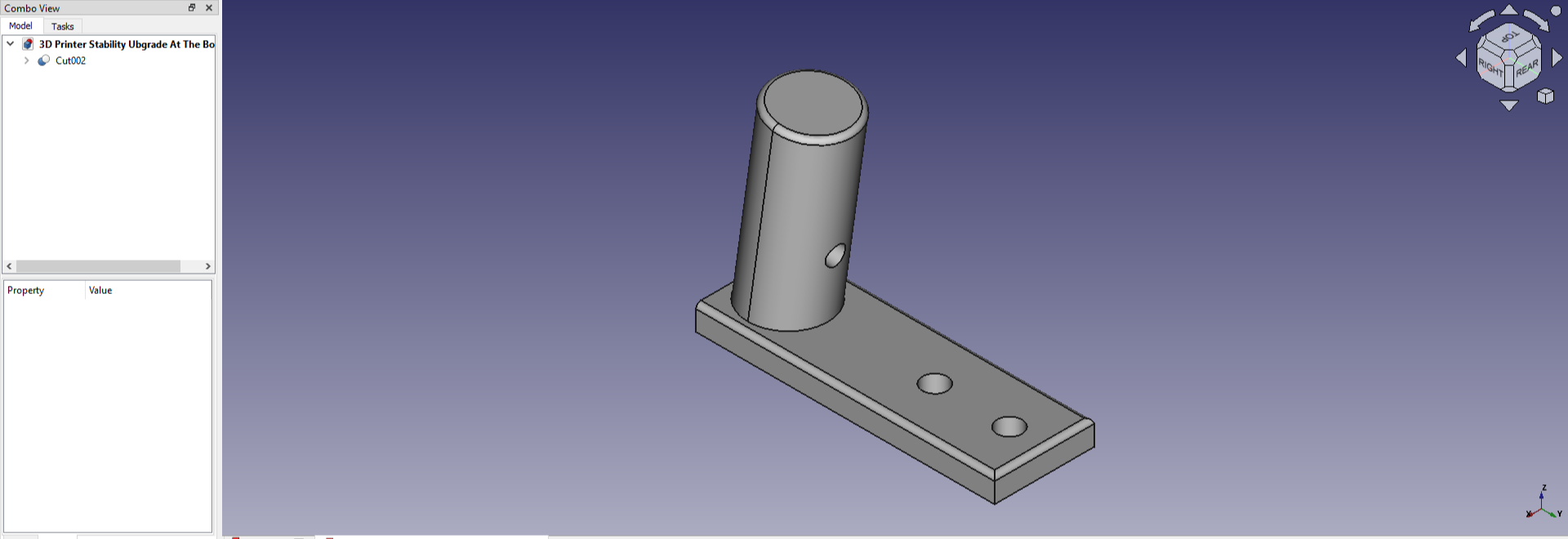
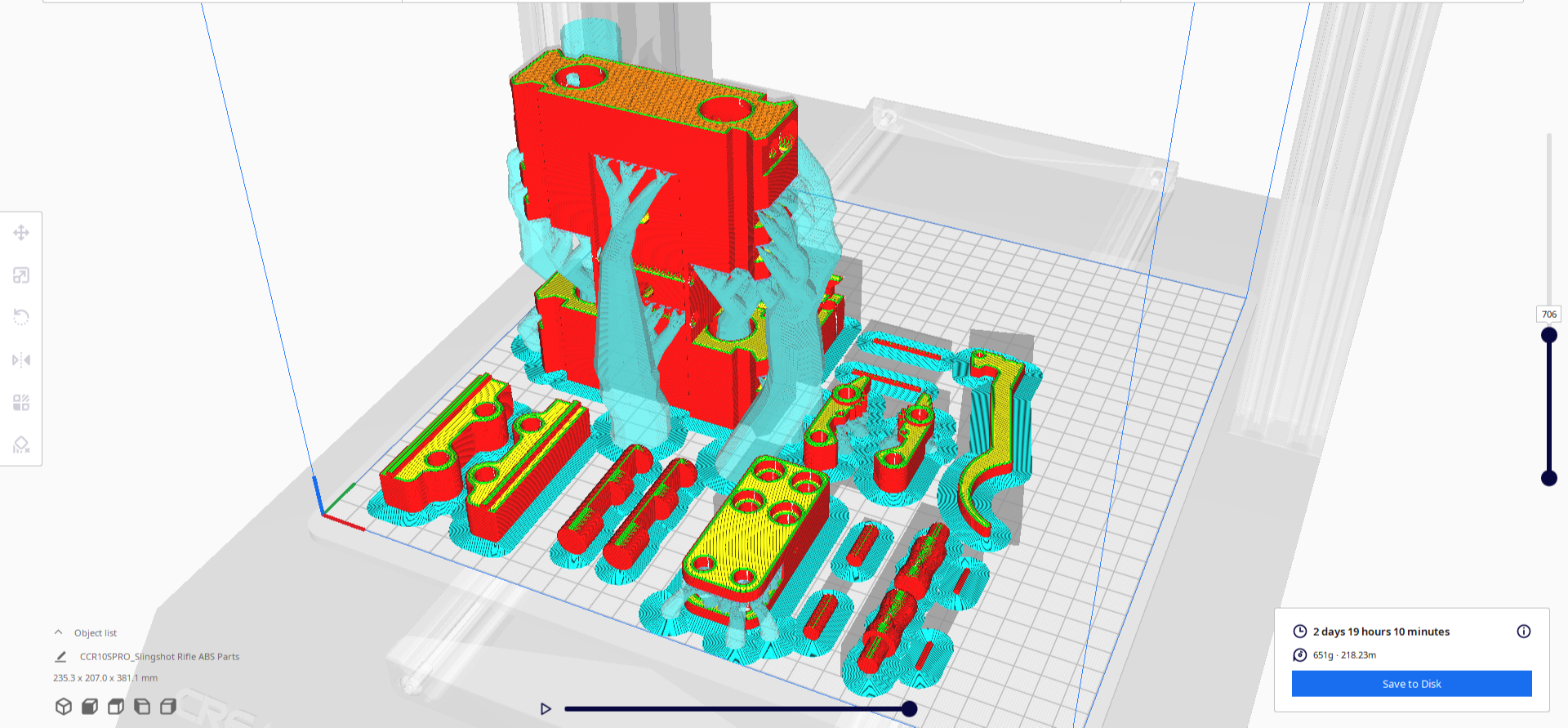
Ultimaker Cura
Throughout my portfolio, CAD projects requiring physical printing have been sliced using Ultimaker Cura. With nearly three years of hands-on experience with this slicing software, I have gained comprehensive knowledge of its intricacies and functionalities. Despite certain inherent limitations, I have effectively maximized its capabilities through meticulous adjustment of settings.